QUALITY ASSURANCE
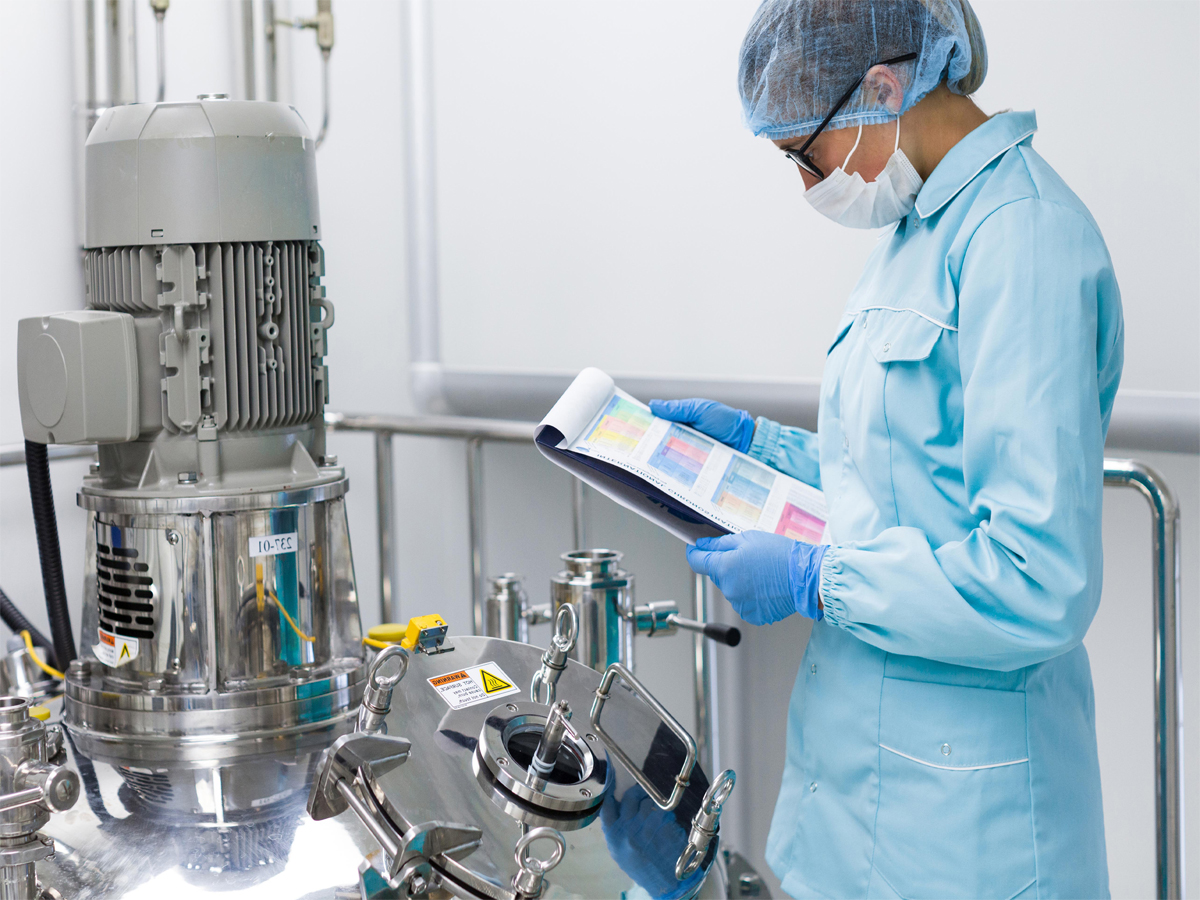
i. Documentation and record Keeping:
Documentation and records are kept to ensure traceability and accountability. This includes Standard Operating Procedure, batch records, specifications, protocols, reports e.t.c.
The preparation, revision and distribution of the documents are controlled by the quality assurance department in coordination with the respective departments. Documents are prepared
on the basis of standard provided in the GMP guidelines given in books and CDs.
The master documents are stored centrally in the quality assurance department and the completed batch sheets are stored in a document store where they are packed properly such that the retrieval can be easily made.
ii. Good Manufacturing Practices (GMP):
GMP regulations provide a framework for manufacturing pharmaceutical products in a manner that ensures their quality, safety and efficacy. QA in the Lomus Pharmaceuticals Pvt. Ltd. Aligns with GMP requirements and involves establishing and adhering to standard operating procedures, hygiene practices, equipment calibration, validation and personnel training.
iii. Quality Risk Management:
QA department are managing risk by following quality risk principles to identify, assess and mitigate risks that could impact product quality or patient safety. Risk assessment tools such as FMEA and Risk ranking and filtering tools are commonly used.
iv. Change control:
QA department are following change control processed to manage any changes that may affect product quality including changes to processes, materials, equipment or facilities, Changes are implemented after thorough evaluation, impact assessment and approval before implementation.
v. Corrective and Preventive actions:
QA department incorporates a CAPA system to address deviations, non-conformances and complaints. Investigation are conducted to identify root causes and appropriate corrective and preventive actions are implemented to prevent recurrence.
vi. Supplier Management:
QA department is following vendor validation procedure for evaluating, selecting and managing suppliers and contract manufacturers. This ensures that the materials and services provided by external parties meet the required quality standards.
vii. Audits and Inspections:
QA department is performing self-inspection once in a six month to assess compliance with quality standards, regulations and company policies. An inspection team is formed comprising of a representative from each of QA, QC, Production and Engineering department to perform self-inspection. Regulatory authorities may also conduct inspections to verify compliance with Good Manufacturing Practices.
viii. Training management:
QA department are providing regular training to all the personnel working in production area and quality control laboratory to make staff more competent. Adequate training programs are implemented to ensure employees have the necessary knowledge and skills to perform their roles effectively and in compliance with quality standards.
ix. Continuous improvement:
QA department is always focuses on continuous improvement by monitoring quality metrices, analyzing data and implementing actions to enhance processes, reduce risks and optimize product quality.
x. Deviation Control:
QA department is following procedure to control planned and unplanned deviation. In case of planned deviation in the manufacturing process which does not affect the final parameters of the product or its quality or its stability, personnel from concerned department initiate the planned deviation format by detailing the cause for deviation. The deviation and justification is checked by the manager of production & planned deviation is implemented only after approval of deviation and justification by QA Department. After implementation of deviation QA review the implementation and ensure that the product complies with specification. If deviation is released to the batch which is for sale batch shall be released only after closure of deviation by QA Department.
In case of unplanned deviation initiator from concerned department incorporate corrective and preventive action based on assessment. The department Head review proposed corrective action and preventive action. After review by Department Head the proposal is forwarded to QA Head for review and approval. Unplanned deviation is implemented only after approval of CAPA by QA Head. After implementation of deviation QA review the implementation and ensure that the product complies with specification. If deviation is released to the batch which is for sale batch shall be released only after closure of deviation by QA Department.